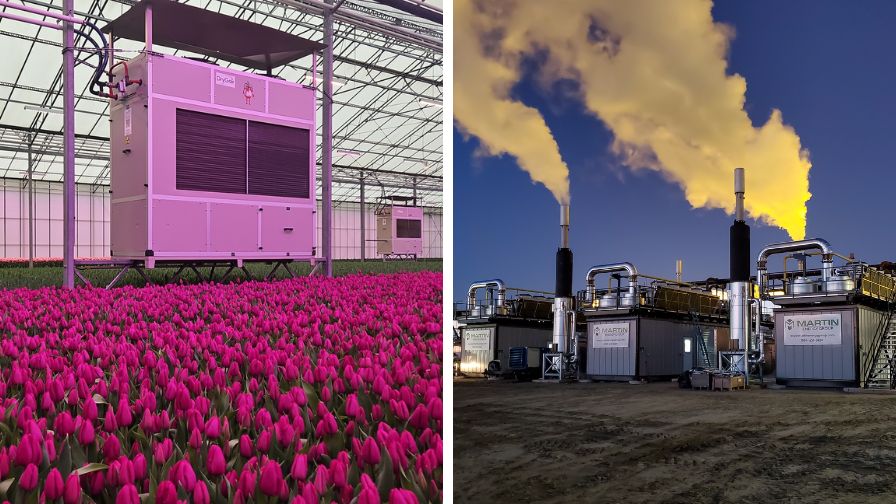
DryGair’s dehumidification solution for tulips (L), and an example of a combined heat and power system with CO2 recovery (R). | DryGair Energies, and Martin Energy Group
Energy efficiency is the game. The price of propane is edging back up. Electricity demand on the grid is skyrocketing with the need to supply data centers, and you know the price per kilowatt hour isn’t going down. Hotter summers, colder cold snaps, and polar vortexes mean growers could use a break on the energy bill. From new high-efficiency, gas-fired heaters to combined heat and power (CHP) systems, here are a few improvements worth considering.
Improvements in Gas-Fired Heaters
High-efficiency boilers, heat pumps, and geothermal aren’t the solution or in the budget for every greenhouse operation. But the old standby gas-fired heaters pushing warm air around the space still work, are still affordable, and better yet, they’ve become very energy efficient. It’s a far cry from the old workhorse hanging in your garage or shop.
Older gas-fired units had gravity vents for exhaust gases. Even units only 10 to 15 years old may still use this older method, which costs money.
“Gravity vent unit heaters manufactured around that time or prior had no power venter in them,” says Richard Boothman, Director of North American Sales at Modine Manufacturing. “Literally, they had a 4-, 5-, or 6-inch stack off the back of the unit going up and out of the greenhouse. That’s how they were built back then. It was fine, and they worked well, but the seasonal efficiency of those units is about 65%.” He explains that although the units run at around 80% (if maintained), the large exhaust hole in the roof reduces that average. “Every time they’re off, you’re losing heat through the stack.”
Newer gas-fired unit heaters have a power vent, closing off that big hole in the roof when the unit isn’t running. And they’ve gained a couple more points in efficiency.
“Our standard gas-fired unit heaters are about 82% to 83% efficient. For every 100,000 BTUs you put in, you get about 83,000 BTUs to use. That’s about as high as you can get with a standard type of combustion [and exhaust] before you start condensing in the flue,” Boothman says.
Enter the relatively new work on efficiency. “A few years ago, we added a new line specifically targeted for greenhouses, which achieves higher condensing efficiency. In a condensing unit, an extra heat exchanger is added. After the air passes over the primary heat exchanger, it goes through a secondary one resembling an air conditioning coil. This secondary heat exchanger extracts a significant amount of heat from the combustion process,” Boothman explains. These units extract so much heat that the combustion byproducts cool to about 130ºF to 140ºF. “With all this efficiency, you’re going to generate a surprising amount of condensate, so you need to run a drain from the unit. This condensate represents the money growers are saving — energy that used to go up the chimney is now being utilized in their space.”
Switching from an older system with a gravity vent, which runs about 65% seasonal efficiency, to a modern condensing gas-fired unit achieving 93%, or sometimes even more, can yield a 30% reduction in energy used. Even switching from the power-vent type to the new condensing gas-fired units can yield energy use reductions of around 18%. Those numbers add up, especially for propane users.

Newer gas-fired unit heaters have a power vent, closing off that big hole in the roof when the unit isn’t running. And they’ve gained a couple more points in efficiency. | Modine Manufacturing Company
As you’d expect, ROI can be pretty quick with such big numbers.
“In some instances, the payback could be two to three years for a heavily used greenhouse, maybe even slightly less. The units come with a 10-year warranty on the heat exchanger, so you’re going to be ahead of the game very quickly,” Boothman says.
Full-scale heating system replacement isn’t needed to harvest energy savings. Growers running gas-fired heaters might have two (or more) in each house, with one serving as a backup to the other. In this case, efficiency savings can be gained by replacing only one of the heaters and setting the new high-efficiency unit as the lead machine, sized appropriately to handle the load. The backup is still there for extreme temps or downtime, but during normal ops, you’re getting all the efficiency of the new heater.
New Hydronic Units
A modern high-efficiency boiler uses a condensing unit, much like described for the gas-fired units, to extract additional energy from the exhaust, raising efficiency. However, using new tech boilers with older hydronic heating units can mask the energy savings. Boothman says, “A standard boiler will put out water at around 180ºF. A modern air-to-water heat pump or condensing boiler runs at peak efficiency delivering water at about 130ºF.” The lower supply water temperature means the hydronic unit needs to be larger, or have more airflow, to maintain the same heating capacity. This means a much larger horsepower fan motor, which consumes a lot more electricity. The fuel bill could drop while the electric bill goes up.
Modine’s Lodronic brand low-temperature hot water unit heater is designed specifically for use with high-efficiency boilers.
“It looks just the same as our standard hydronic unit heaters,” says Boothman. “But within the cabinet is a four-row coil.” Most hydronic units have one row of coils. With the new unit, the air is in contact with the heat exchanger tubes for much longer, pulling more heat out of the water and passing it on to the air. The unit creates a larger temperature delta between the incoming and exhausting air, reducing the volume of airflow needed to heat the space. Less airflow required means a smaller fan motor. The same idea goes for cooling. With a chiller supplying chill water or a heat pump running in reverse, the unit can also cool the space.
Ventilation Improvements
For years, humidity in the greenhouse has been controlled using ventilation — propping the windows open or running some fans. But ventilating for humidity control is energy intensive. Depending on the season, fresh air must be heated, and the warm air you paid to heat just goes out the window. Actively managing humidity separately from temperature can significantly lower energy costs.
“We are separating temperature from humidity. One influences the other, of course, but when you can isolate and deal with each parameter separately, you can invest the energy in a much better way,” says Hadar Fuchs-Rubal, Chief of Sales at DryGair. “Once you have real control over humidity as an independent parameter, heating energy can be focused on creating the exact amount of temperature needed.” Actively dehumidifying also provides control over VPD (vapor pressure deficit), without needing to adjust the temperature of the space.
Active humidity control reduces the energy needed to maintain temperature as well.
“It’s a concept of keeping your greenhouse closed, extracting the excess moisture, and maintaining airflow in the space,” says Douglas Miller, Sales and Marketing Director for North America at DryGair. “Opening vents for humidity control allows all that warm air to leave, taking moisture with it. But when the vents are closed again, the whole compartment is colder, so it must be heated again. It’s like blowing dollars out the door.” For those who operate at a higher-than-ambient level of CO2, running a more closed system is also beneficial.
Co-Gen Power Systems
What if you could own your utility services? Electricity and heat, all in one fell swoop. Cogeneration — or combined heat and power — also called CHP, places the electrical generation onsite at your facility. The large efficiency gain comes from recovering the generator’s waste heat and using that heat in the greenhouse.
The common CHP system is an internal combustion engine driving the generator. They’re normally natural gas fueled, although they can be propane. Usually, about two-thirds of the energy used to generate electricity is lost as heat. With a CHP system, that heat is captured for use in the greenhouse.
“CHP systems achieve high efficiency through comprehensive heat recovery. We recover heat from multiple sources: jacket water, exhaust, oil, and intercooler systems. Using single-pass exhaust recovery technology, we can achieve efficiency rates exceeding 90% — similar to high-efficiency furnaces,” says Kevin Rohrer, Strategic Account Executive at Martin Energy Group.
While it might seem like these systems are only for the big players, technology and manufacturing improvements have brought them down in size for more modest-sized operations.
“The smallest viable systems start at 150 kW, with 300 kW being a sweet spot for beginners. Economies of scale improve with larger systems, but smaller operations can see significant benefits, especially with rising power prices and demand charges,” Rohrer says. ROI is typically three to five years but varies with fuel prices and potential rebates.
CHP systems offer additional benefits for those considering expansion or new construction.
“The two main factors are controlling power costs and addressing grid power availability limitations. Many facilities face either insufficient grid power or prohibitively expensive line upgrades costing millions of dollars,” Rohrer says.
CHP systems may be the less expensive option when those costs are considered, providing power, heat — even chill water for cooling with an absorption chiller system — and independence from rising electricity rates, brownouts, or outages.